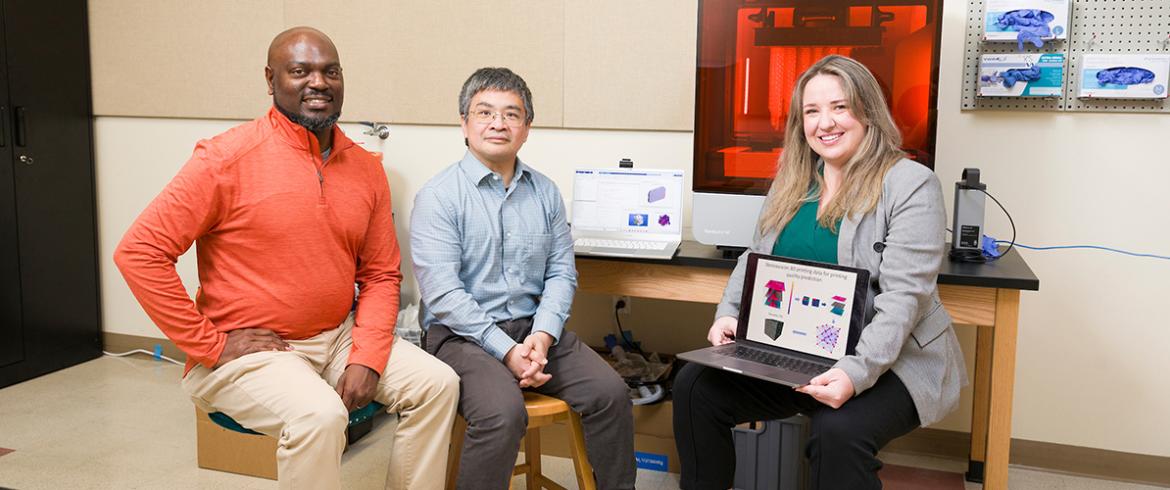
From left, Associate Professor Tarik Dickens, Associate Professor Hui Wang, and Assistant Professor Rebekah Downes pose in a lab in the High-Performance Materials Institute in the Materials Research Building at FAMU-FSU College of Engineering. The team, led by Wang, has been awarded over $2.2 million in funding from the Air Force Office of Scientific Research to use artificial intelligence technology to advance defect detection in powder-based additive manufacturing. (Scott Holstein/FAMU-FSU College of Engineering)
FAMU-FSU College of Engineering researchers are leveraging artificial intelligence to develop advanced defect detection tools for powder-based 3D printing, supported by a $2.2 million Air Force grant.
The team, led by Associate Professor Hui Wang, is collaborating with Pennsylvania State University and HP Inc. to implement combinatorial generalization (CG) techniques that significantly improve defect prediction models in additive manufacturing processes.
“Combinatorial generalization represents a computational reasoning capability that supports next-generation AI by mimicking human recognition behavior that generates new knowledge from data,” Wang said. “It is exciting to use this emerging technology to solve difficult manufacturing puzzles.”
Advancing Metal 3D Printing Technology
The research focuses specifically on binder jetting, a 3D printing technique that uses liquid binding agents to fuse powdered materials. This method is critical for creating complex, high-performance components with intricate geometries and offers higher productivity than alternative metal printing technologies.
Powder-based fabrication serves numerous industries, including aerospace, automotive, healthcare and defense, where complex metal components are essential.
Tackling Key Manufacturing Challenges
One significant challenge in powder-based fabrication is understanding material porosity—the formation of tiny holes resulting from powder spread and powder-droplet interactions, which can compromise structural integrity.
The researchers are implementing combinatorial generalization to enable AI systems to make inferences about new scenarios based on knowledge learned from multiple data sources. This approach mirrors human cognition, where existing knowledge and patterns lead to innovative solutions.
“This technology could democratize manufacturing, making it easier for inexperienced manufacturers to advance from lab testing to large-scale production,” Wang said.
Collaborative Research Environment
The project draws strength from a diverse team including graduate students, postdoctoral researchers, and faculty collaborators Tarik Dickens and Rebekah Downes from the Department of Industrial and Manufacturing Engineering. External collaborators include Jun Zeng, who leads the Physics AI engine group at HP Inc.’s additive manufacturing R&D Lab and Penn State University Professor Jingjing Li.
AFOSR funding will help acquire essential experimental materials and small-scale testing equipment. Penn State researchers provide critical simulations and XCT data modeling support. At the same time, HP Inc. offers access to data from their 3D Printing and Digital Manufacturing Center of Excellence, high-performance computing resources and student internships.
Future Implications
This interdisciplinary initiative demonstrates the potential of combining industrial and manufacturing engineering expertise with cutting-edge artificial intelligence capabilities.
“AFOSR programs in computational mathematics and physical sciences are actively seeking novel solutions in machine learning for scientific discovery and our project aligns well with this vision,” Wang said. “We expect that our discoveries will significantly enhance the ability of Department of Defense researchers to efficiently leverage various data sources and expedite the development of new manufacturing processes and materials. It’s exciting to see what lies ahead and where this research will take us.”
Editor’s Note: This article was edited with a custom prompt for Claude 3.7 Sonnet, an AI assistant created by Anthropic. The AI improved clarity, structure and readability while preserving the original reporting and factual content. All information and viewpoints remain those of the author and publication. This disclosure is part of our commitment to transparency in our editorial process. Last edited: 04-07-2025.
RELATED ARTICLES
Researchers Improve 3D Printing Quality with Between-Machine Experience Transfer
Engineering researchers develop innovative technique for 3D printing using magnets
Layer By Layer: Professor Develops New 3D Printing Technology