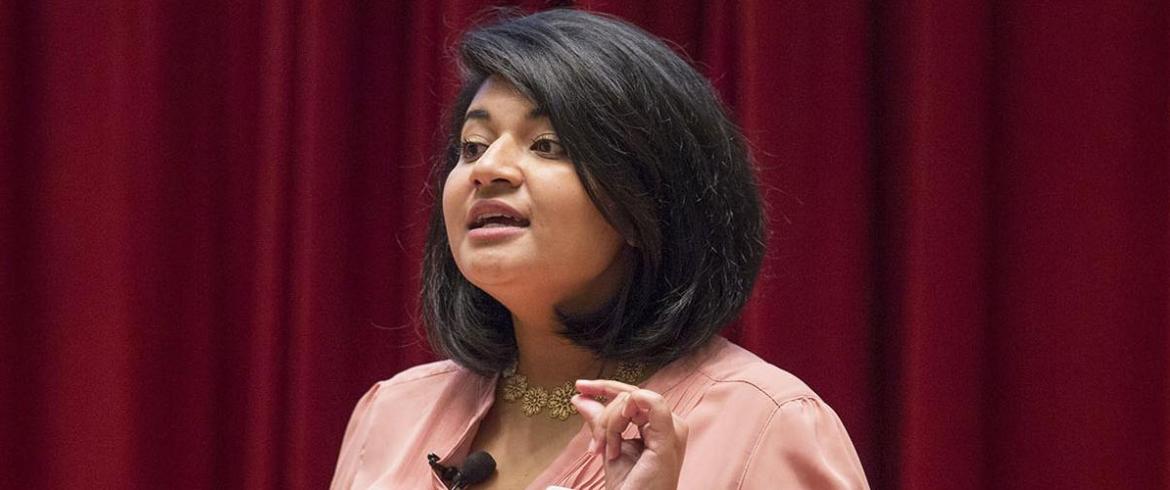
Madhuparna Roy, a Spring 2020 engineering doctoral graduate and the lead author of a paper that showed the possibility of using magnets to realign fibers inside a material being used for 3D printing.
Researchers from the High-Performance Materials Institute, FAMU-FSU College of Engineering have developed and investigated a new technique for 3D printing that could produce much stronger materials that could be used in a variety of engineering applications.
In a paper published in the journal Additive Manufacturing, Madhuparna Roy (a Spring 2020 Florida State University Ph.D. graduate from the college) and advising professor Tarik Dickens, Ph.D. showed the possibility of using magnetic fields near a 3D printer to change the alignment of fibers inside an object as it was being printed—a term Dickens calls ‘magneto-assisted printing’. This tweak in the mechanical properties of the material could greatly improve its overall quality and strength.
“3D-printed materials are not strong on their own because they’re just plastic layers sitting on top of each other,” said Roy, the paper’s lead author. “The gap in the research world is to improve mechanical properties. With improved mechanical properties, you could create solutions for any kind of application, depending on what that particular application requires.”
3D printing is a relatively new manufacturing technology. It has grown significantly because of the availability of different types of printing and different materials that can be used with the technology. A wide variety of items are already being 3D-printed, including musical instruments, houses, medical equipment and parts needed in manufacturing.
Because the technique is still so new though, researchers are still finding ways to improve the process.
3D printing sometimes adds fibers made from various materials to the plastic or other substances used in printing, a technique that can improve the strength of the finished piece. When those fibers come out of a nozzle, they are oriented parallel to the direction of the flow from that nozzle. But by applying a magnetic field near the printer, the researchers were able to create objects with fibers oriented perpendicular to the nozzle’s flow.
The alignment of fibers inside an object can give it certain properties that scientists or engineers might find useful. For example, a printed object with the fibers oriented in certain alignments could be structurally stronger than one made normally. Or engineers might want a 3D-printed part that is well-suited for conducting electricity, which they could make by aligning conductive fibers inside a material.
Along with showing the possibility of this technique, the research also examined how different flow rates, magnetic field strength and the shapes of nozzles affected the ability to change the fiber alignment. A theoretical model developed by FSU assistant professor of scientific computing Bryan Quaife, was used to study the process regime of the assisted flow-geometry. The study found that the more viscous the printing substance, the stronger the required magnetic field for realigning the magnetic fibers. The experiments also seemed to show that as the material is moved through the nozzle faster, the less the interior fibers will be realigned—potentially improving the printability as a consequence.
This paper showed the possibility of using this technique for a material with low viscosity, so future investigations could study the process with a more viscous material that requires a stronger magnetic field to realign the interior fibers, Roy said. Mechanical tests of the finished 3D-printed product would also be helpful.
“There are still plenty of gaps that need to be addressed in terms of what materials can be used and what printers can be used in conjunction with them,” Roy said. “In this work, we’re talking about using plastics with metal particles in them. We’re combining the two major groups of 3D-printing materials to make a new material that gives you added functionality when it comes to making anything else.”
Co-authors of this study include FAMU-CREST postdoctoral researcher Phong Tran, Ph.D., and Bryan Quaife, Ph.D. FAMU-FSU College of Engineering Associate Professor Tarik Dickens is the corresponding author and principal investigator of the funded work.
This project was supported by the National Science Foundation CREST Center for Complex Materials Design for Multidimensional Additive Processing (#1735968).