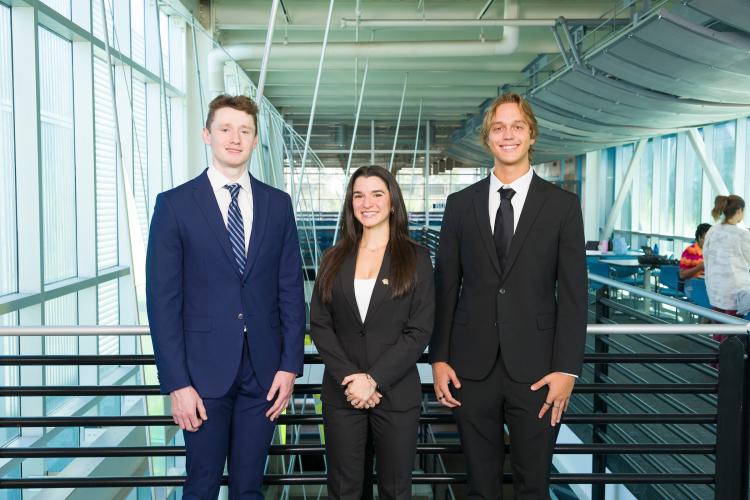
Concrete construction is expensive, time-consuming and harmful to the environment. This method produces a lot of carbon dioxide, which is detrimental to the atmosphere. In this project, we looked at using 3D-printed concrete as a building material. We made all the walls of a four-story house with 3D printing, eliminating the need for pre-casting or formwork.
The advantages of 3D-printed concrete include faster construction, lower costs and better sustainability. Because this method is still new, there aren’t many established design standards. We talked with experts to find the best way to analyze this complex structure. We used computer design software to analyze how structurally sound the building was and how it performed under expected loads.
Our design includes 3D-printed concrete walls, cast-in-place concrete slabs and steel-reinforced concrete beams. We also included a deep foundation utilizing Auger Cast piles, which provided good bearing strength in sandy soils. Using material properties specific to 3D-printed concrete set in the American Concrete Institute standards, we looked at stress distribution, deflection and failure modes. The house has a unique shape, which required careful planning to ensure stability.
We focused on optimizing the design for durability, ensuring that the structure could resist the harsh coastal environment on the Bob Sykes Cut of St. George Island in Franklin County, FL, while keeping aesthetics in mind. This research added to the understanding of new construction methods and highlighted how 3D printing could create sustainable buildings near coastlines.
Patrick Camden, Natalija Nikolic, Logan Weslar
O. Sean Martin, Ph.D., P.E., Pedro Fernandez-Caban, Ph.D., Primus Mtenga, Ph.D., P.E., Kamal Tawfiq, Ph.D., P.E.
Kever McKee – Barry Pujol
Fall