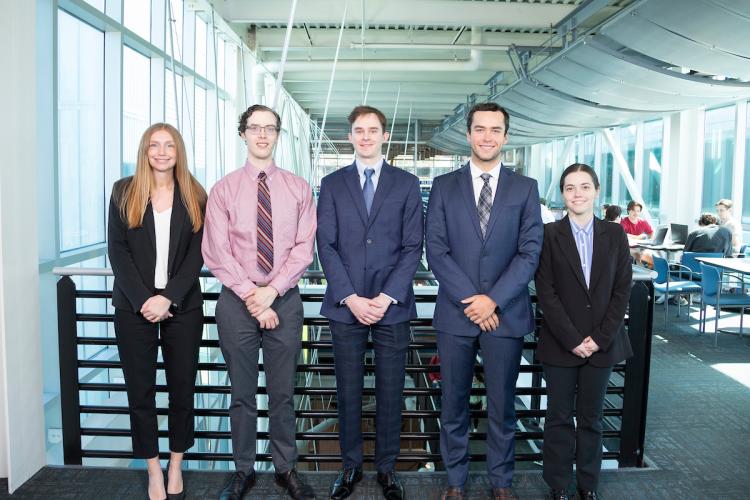
The US Energy Information Administration estimates that up to 30% of natural gas (NG) reserves are flared into the atmosphere, producing an average of 111,000 metric tons of CO₂ per year. NG is primarily composed of methane and is flared to create CO₂, which is a less potent greenhouse gas. NG is often flared when it is stranded in an isolated location, making recovery economically unviable. To combat the under-utilization of NG as an energy resource, we designed a modular process to harvest and convert it into useful, liquid fuel products.
Modular processes combine various unit operations into singular “modules,” which can be prefabricated before deployment on-site. We designed three module sizes to receive 500, 2500, or 5000 MSCF/day of NG directly from a remote wellhead and produce fuel intermediates. The modules take advantage of “numbering up,” which uses multiple smaller modules to create the throughput of one larger unit. This also allows for flexible redistribution of smaller units as wellhead production declines over time.
Our modules include a syngas unit that converts NG into syngas, a mixture of H₂ and CO. The syngas is then fed to a Fischer-Tropsch (FT) reactor which catalytically links carbon units into liquid hydrocarbon chains. We chose a microchannel FT reactor over a conventional packed bed reactor for its improved energy efficiency and higher syngas conversion. The liquid fuels are then separated into usable product ranges, which are then transported offsite to a processing plant for blending and distribution.
Our safety analysis revealed that based on OSHA component classifications, many of the chemicals in this process are hazardous, with flammability as the main concern. We considered safety implementations for operating conditions, transportation and storage hazards. We conducted the safety analysis in conjunction with process design to ensure ethical design choices and adherence to inherently safer design (ISD) concepts.
Our financial assessment included analyses of individual modules, initial deployment and redeployment, and other associated costs. Net present value (NPV) is a metric that shows how the value of an investment will change over time. Our secondary goal was to maximize net present value (NPV) with respect to the deployment and redeployment of our modules. We used CAPCOST to evaluate the overall profitability, which modeled NPV with respect to capital and operating costs.
Brooklyn Ford, Josiah Lopez-Poindexter, Michael Merino, David Quirie, Alexis Tallon-Rendon
Robert Wandell, Ph.D.
FAMU-FSU College of Engineering
Spring