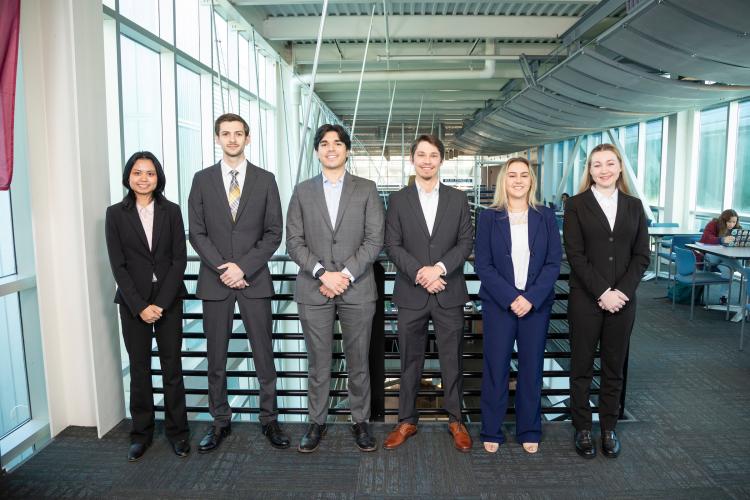
Our goal was to create a safe and long-lasting total stemless reverse shoulder arthroplasty implant that can be approved by the FDA for consumer use. This type of arthroplasty would allow for a large range of motion compared to current models. However, the humeral component is more easily dislodged from the bone. We created a testing rig to apply force at various angles to mimic stresses from moving the arm.
To compare models, we used the maximum force at failure using a fixed sensor and the number of iterations at 20% of the max force. Our models were decided through modifications on the Exactech Equinox® model to increase contact area, allow for easier insertion and resist rocking motion. The models created were thinning the fins to a sharp edge at the bottom of the component and orienting the fins into a ‘T’ shape so that all fins are 90° to each other at the center. Stress vs. strain graphs may also be utilized for further comparison.
Results for testing the fins used for a reverse stemless arthroplasty procedure have yet to be obtained. The aim is to utilize these results to successfully display the implantation’s capabilities. Results are helpful in showing how well the humeral component of the stemless reverse design remains stable in the bone. The number of iterations before failure is indicative of the lifespan of the implant component before dislodgement. The results also show the comparative success of the three different designs to each other for bone-component stability.
Angelina Lahn (BME), William Wartman (ME), Santiago Lazarte (BME), John Sorensen (BME), Taylor Vanderlinden (BME), Kiersten Cady (ME)
Stephen Arce, Ph.D.
Dr. Tom Vanasse, Exactech, Inc.
Spring