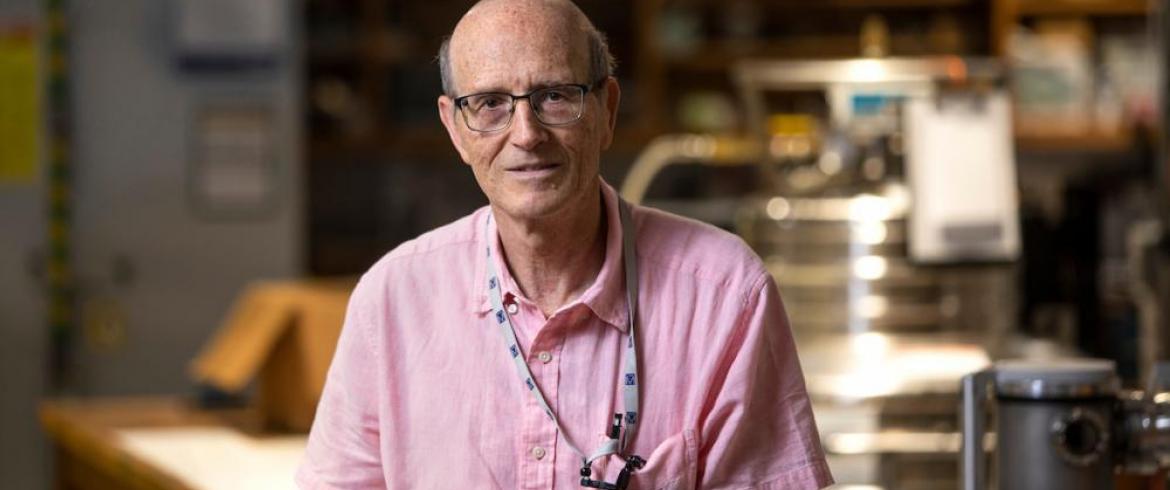
Theo Siegrist, professor of chemical and biomedical engineering at the FAMU-FSU College of Engineering, stands in his lab at the National High Magnetic Field Laboratory where he studies the atomic arrangement in crystalline materials. (Photo: FAMU-FSU Engineering/M Wallheiser)
New research shows critical changes to the microstructure of iron-based alloys, materials that are important for manufacturing permanent magnets for use in electrical appliances and cars.
Magnetic materials play a crucial role in the progress of industrial growth and societal advancement. They are used in everything from electric motors and generators to actuators and are important in energy conversion.
In a new study, researchers from the FAMU-FSU College of Engineering, National High Magnetic Field Laboratory and the School of Materials Science and Engineering at Northeastern University in China, are collaborating to understand the effect of the magnetic field on the microstructure of magnetic materials. Their findings may improve the ways these materials are processed and ultimately perform.
Scientists are interested in the microstructure of these materials because it can be shaped for tuning magnetization. By influencing and controlling the microstructure, scientists can control both the magnetic and mechanical properties of the substance.
“We have found that an external magnetic field can drive changes to the microstructure of the specific alloys of iron (Fe), chromium (Cr) and cobalt (Co) used for magnet-based materials,” Theo Siegrist, a professor of chemical and biomedical engineering at FAMU-FSU Engineering and National MagLab researcher, said. “The application effects the hardness of the alloys when heat is applied.”
The joint research was on Fe-Cr-Co alloys because they can be shaped easily and have better machinability than Neodymium (Nd)-based magnet materials. Magnet materials composed of Fe-Cr-Co are suitable for use in small devices where accurate dimensions and complicated shapes are required. The alloys are used in wires, tubes, bars and shapes used in motors for electrical appliances and cars.
“We used an atomic resolution electron microscope to get an unprecedented close-up picture of the microstructure of the alloys,” Ke Han, a research faculty member of the National MagLab, explained. “The microstructure is responsible for the mechanical properties, such as hardness.”
Using the specialized microscope, the researchers investigated the effect of a 3-Tesla magnetic field on the microscopic decomposition of the alloys at elevated temperatures. For comparison, a 3-Tesla field is about 60,000 times stronger than the earth’s magnetic field. They studied the microstructure using aged samples.
Heat treatment of materials under external magnetic field is known as magnetic thermal heat-treatment. The technique strengthens solids, like metal or glass, by raising, maintaining and then slowly reducing the temperature. The process can enhance the performance of magnetic devices and materials.
The team discovered that by applying heat while in the magnetic field, the alloys developed desirable characteristics such as hardness and the ability to be machined and shaped. Materials that can be shaped while retaining hardness are desirable for manufacturing permanent magnets.
“The 3-Tesla magnetic field decreased the hardness somewhat but strongly increased the ductility of the alloys,” Siegrist said. “The change in hardness values is attributed to the composition fluctuations of iron, chromium and cobalt in nanometer scales.”
Their research was recently published in the Elsevier Journal of Materials and Design.
“The mechanical properties and data generated from the study are of interest to people in the industry who want to improve the performance of the materials,” said Zhaolong Xiang, a graduate student from Northeastern university who previously worked in National High Magnetic Field Laboratory. “The data is also of interest to metallurgists working on the magnetic field processing of alloys.”
“We expect more work will be undertaken to study the decomposition in these materials,” Siegrist said. “The external magnetic field provides a simple way of tuning the mechanical and magnetic properties of the alloy system.”