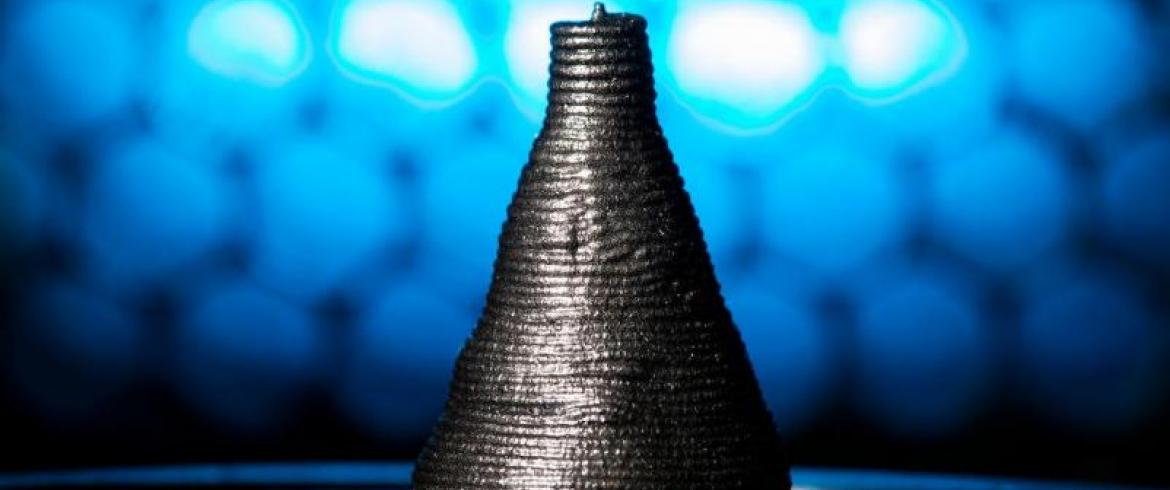
As part of a new $5 million NSF study, FAMU-FSU Engineering professor Subramanian Ramakrishnan aims to 3D-print lightweight conductive composites to study the effect of printing conditions on particle orientation and final composite performance. These materials have defense and other applications. (Photo: FAMU-FSU Engineering/M Wallheiser)
Researchers at the FAMU-FSU College of Engineering have discovered they can influence and increase the electrical performance of composites infused with graphene nano-platelets in a National Science Foundation (NSF) study that could change the way materials are designed and manufactured.
Their research is highlighted in the journal Additive Manufacturing, a peer-reviewed publication that reviews innovative research papers in additive manufacturing.
Subramanian Ramakrishnan is a professor in chemical and biomedical engineering at the college and is the lead investigator for the study. He is collaborating with researchers from industrial and manufacturing engineering and the Air Force Research Laboratory to conduct the work. Funding from the project is supported in part by a $5 million grant from the NSF.
“Our aim is to 3D-print lightweight conductive composites and to study the effect of printing conditions on particle orientation and final composite performance,” Ramakrishnan said. “The combination of epoxy resins and graphene nano-platelets is of interest in several applications for the Air Force, such as thermal interface materials, heat sinks, and electromagnetic shielding materials.”
The composite the Ramakrishnan’s group is studying is useful for thermal interface materials, shielding materials for electronic devices, and light-emitting devices.
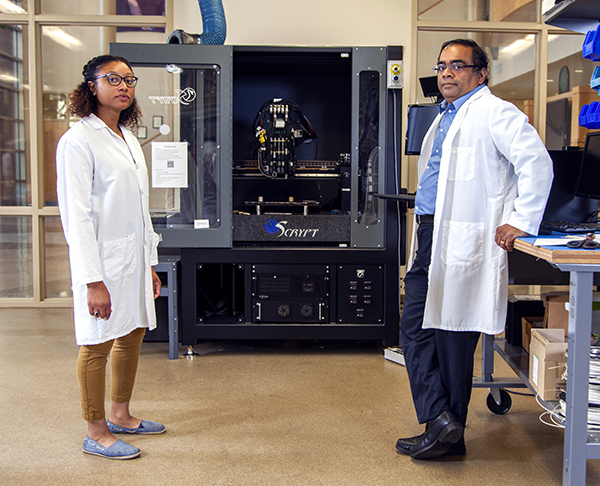
The researchers use direct ink writing, an additive manufacturing technique that can assess the qualities of the composites. How well the substance performs is directly related to print techniques, specifically, the speed of the print and the number of graphene nano-platelets infused in the composite.
Engineers like the composites because they have favorable mechanical characteristics, like strength and stiffness, and have the potential for zero or near-zero coefficient of thermal expansion, according to the study.
“We are using direct-ink writing, an extrusion-based additive manufacturing process where we are working with materials on a micro-scale,” Roneisha Haney, a doctoral student researcher on the project, explained. “The liquid phase ink is dispensed out of small nozzles under controlled flow rates along digitally defined paths to fabricate a 3D structure, layer by layer.”
One observation that the research revealed is that the printing process effects the orientation of 2D particles during printing. At certain speeds, the particles arrange themselves in such a manner that they line up vertically and develop optimal properties of strength and stiffness. The gap height, nozzle speed, extrusion pressure, line width, and nozzle diameter influence the final properties of electrical conductivity the material exhibits.
“We found that a wide-range of matrix filler combinations allow for versatility in the properties of the printed material,” Ramakrishnan said. “By fine tuning the way they are processed we can suggest guidelines to maximum effectiveness and performance of the composites which are used in the development of several functional materials and devices.”
The study helps define design rules for the improvement of the overall performance of graphene-based composite structures and provides insights into the parameter of print speed that will be critical in expanding the applications of these composites in the future.