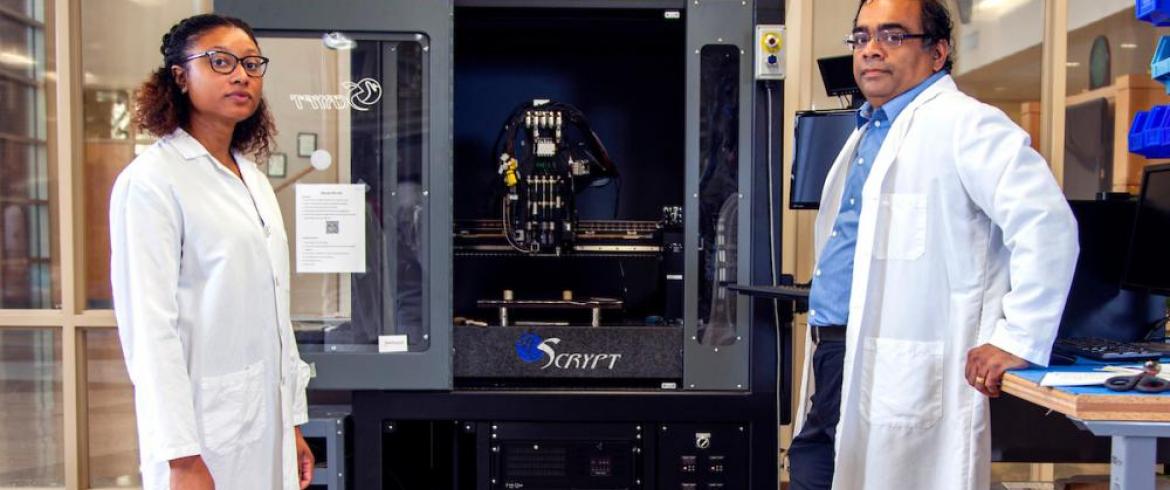
Roneisha Haney, Ph.D. and Professor Subramanian Ramakrishnan of the FAMU-FSU College of Engineering use the nScrypt laser 3-D printer to research additive manufacturing of complex materials for the Pentagon and others. (Photo: FAMU-FSU Engineering/M Wallheiser)
3-D printing may still seem to be a truly futuristic technology, but how it will ultimately change product design, manufacturing and delivery remains an exciting horizon we are only starting to fully imagine.
“If you look at the evolution of the smartphone, you can see where 3-D manufacturing is going,” Ken Church, CEO of nScrypt, a high-tech 3-D equipment company, said. “Phones at first were used just for talking, now the smartphone technology has replaced everything from a GPS to a digital camera.”
Florida-based nScrypt specializes in high-precision, micro-dispensing, direct digital manufacturing and provides specialized 3-D printers for FAMU-FSU College of Engineering researchers who are improving materials and processes using nanotechnology.
Church, who spent his career printing electronics on unexpected surfaces, explains, “3-D manufacturing will become much more than we can imagine.”
Subramanian Ramakrishnan, professor of chemical and biomedical engineering and Tarik Dickens, associate professor of industrial and manufacturing engineering, lead research groups using the printers for additive manufacturing composite research. They are director and associate director, respectively, at the FAMU CREST Center for Complex Materials and Design (CoMand).
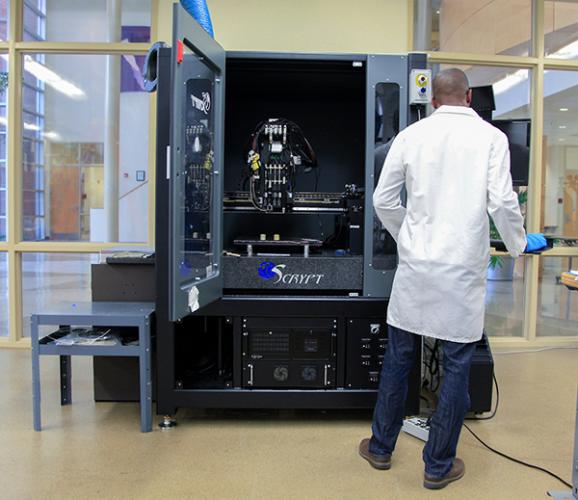
The researchers were recently awarded $660,000 from the U.S. Department of Defense (DoD) for composites studies. Polymer (resin) matrix composites are lightweight and can withstand extreme temperatures. The Pentagon is interested in these materials as thermal interface materials, heat sinks and electromagnetic shielding material.
“We are advancing research in polymer matrix resins,” Ramakrishnan said. “The printers have the capability to print a wide-range of matrix filler combinations. This allows for versatility in the properties of the printed material.”
The first 3-D printer at the college was procured in the late 1990s by professor Yaw A. Owusu and housed one of the nation’s first Stratasys Dimension units. The world of additive manufacturing has grown to near 25% compound annual growth rate over the past few years and has recently found newer applications during the COVID-19 epidemic.
“We currently have three high-precision nScrypt 3-D manufacturing systems at the college, allowing us to print multi-materials with unique gizmos and proprietary printheads,” Dickens said. “Precision becomes important when manufacturing goes to a much smaller scale, such as electronics.”
One of the advantages of 3-D printing and 3-D manufacturing is the processes allow the user to print on different kinds of materials. Everything from plastics, photosensitive resins and ceramics, to thermoplastic composites infused with carbon nanotubes and fibers and even stem cells can be 3-D printed.
So how does the printer accommodate all these substances?
“We have something like a toolbox that allows for multi-materials to be printed using multi-processes,” Church said. “We take micro-dispensing, 3-D printing, milling and other processes and put them all on a signal tool plate called a penta-head, and put this inside a single system that allows us to process multi-materials in a single device.”
The print process itself is of interest to the scientists in the quest to improve additive manufacturing techniques.
“We are asking the question of why and how things happen,” Ramakrishnan said. “We want to know how to develop novel materials, and help to advance design rules for processing.”
In one study funded by the U.S. Air Force, Ramakrishnan’s group used an additive manufacturing technique called direct ink writing to assess the qualities of composites. The scientists discovered the electrical performance of composites is directly related to print techniques. Specifically, related to the speed of the print and the number of graphene nano-platelets infused in the composite.
“In the USAF study, we used an extrusion-based additive manufacturing process and worked with materials on a micro-scale,” Roneisha Haney, Ph.D., a former researcher on Ramakrishnan’s team, explained. “The liquid-phase ink is dispensed out of small nozzles under controlled flow rates, along digitally-defined paths to fabricate a 3-D structure, layer by layer.”
By fabricating layer by layer, the printer can provide quantitative data about each step of the process. Haney was recently been hired by the Materials and Manufacturing Directorate at Wright Patterson Air Force Base for her expertise in additive manufacturing and materials characterization.
“By fine-tuning the way composites are processed, we can suggest guidelines for maximum effectiveness and performance when used in the development of several functional materials and devices,” Ramakrishnan said.
In another study funded by the National Science Foundation, Dickens’ research group made novel discoveries related to routine printing and assisted processing.
“In January 2020, we published research on the use of magnetic-responsive inks and assisted-print head devices to control the morphology and orientation of functional particles,” Dickens said. “This could pave way for more multi-processing for direct-write and printing applications.”

Dickens’ group is part of a project supporting NASA’s mission to bring humans to Mars.
“We’re designing next-generation materials that will take us to Mars,” Dickens said. “When we get to Mars—or even before—we will need to have habitats, functional devices and working equipment. 3-D printing will 100% be part of that.”
Currently, nScrypt has a 3-D bioprinter aboard the International Space Station. This Bio-Fabrication Facility is a 3-D bioprinter used to print adult human cells and adult tissue-derived proteins into tissue structures.
3-D printing and 3-D manufacturing are evolving quickly. To meet the needs of this evolving technology, the college created a physical lab space of concentrated advanced additive nanomanufacturing instrumentation, which opens in the fall of 2021. The lab, located in the Florida State University High-Performance Materials Institute (HPMI), is an expansion of the National Science Foundation (NSF)-supported Florida A&M University CREST CoMand that Ramakrishnan and Dickens lead.
“The research workforce in advanced manufacturing is critical to the U.S. in its re-emergence in manufacturing, innovation and economic vitality,” Dickens said. “We are building the future workforce in the education of undergraduate and graduate students in an area of national need.”