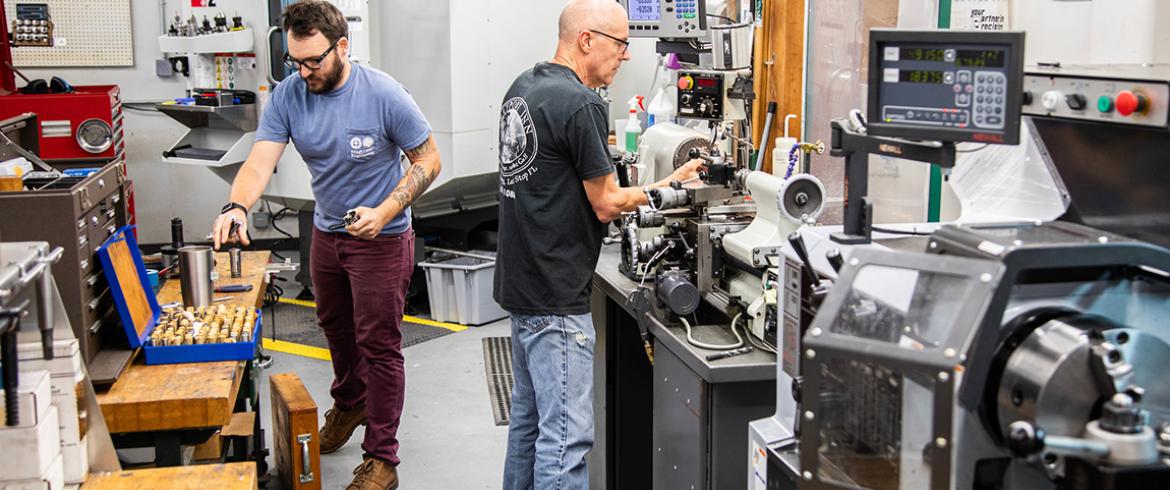
FAMU-FSU College of Engineering machine shop technicians Tom Slade, right, and Justin Pogge work in the machines in building A. (M Wallheiser/FAMU-FSU Engineering)
The FAMU-FSU College of Engineering Machine Shop crew kicks into high gear when senior design rolls around.
Students count on the small team of superheroes to support their capstone projects. For many, those projects represent the highlight of their college careers.
“There’s a saying, ‘measure twice, cut once,’ but the joke is measure twice, cut twice,” Jeremy Phillips, the manager of the FAMU-FSU College of Engineering Machine Shop, said. “We encourage students to think things through on paper and use CAD software before requesting us to spend the time and expense machining a bad part.”
Phillips says the students must understand if they design a part and get it machined or manufactured for a company in the real world, a mistake could cost the company thousands of dollars. That dose of reality is part of the student’s learning experience.
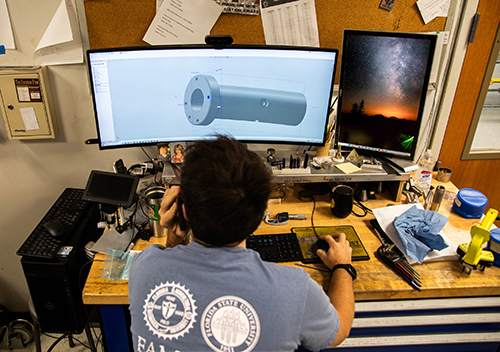
“We want to add to their educational experience and help them be successful,” Phillips said. “If we see a problem with their design, giving alternatives is an important part of what we do. We do not want to discourage their ideas, but we need to see if their design is machinable.”
The measurements the machinists work with are tiny—like if you split a human hair into three pieces. Then take one of the pieces and divide it into ten pieces. The slightest error can ruin a part, causing it not to work as intended. Precision is key.
“We work with tight tolerances, the difference of maximum and minimum permissible errors allowed in measurement. The numbers must be precise regarding machining parts, or they will not be accepted by the end user,” Phillips said.
That Can-Do Attitude
That precision goes into every aspect of the machinists’ lives and lends itself to excellence in even the hobbies Phillip’s team, Justin Pogge, Wade Robinson and Tom Slade, engage in. From roasting the best coffee bean to building espresso machines, the group finds joy in, “doing it right,” a mantra that good machinists understand.
Laurie Herring, a senior designer at the college who regularly works with the group for communications projects, explained, “Last year, we did FIRST Robotics at the Al Lawson Center, and there was no way to roll the robots into the facility. Without hesitation, the guys designed a ramp so the kids could roll their robots in. It’s a classic example of how they solve problems when you need them the most. There is nothing they won’t do for us. They are so handy that they can make stuff from scratch if they have the raw materials.”
The shop fabricates and assembles custom-designed parts and prototypes for FAMU and FSU students, faculty, and staff in all the departments at the College of Engineering. The work they do is especially appreciated when it comes to research support. They are well equipped for machining and fabricating most any project requested.
“Most machine shops do not want to make one-off custom parts,” Phillips said. “If you can find a shop to do that, it can cost thousands of dollars and take months to receive parts. We strive to be efficient and produce high-quality parts in a timely manner with no labor cost, giving our professors the edge compared to a lot of universities.”
High-Tech Handicraft
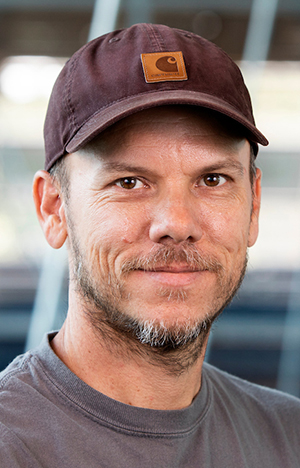
“The FAMU-FSU College of Engineering Machine Shop was a crucial part of establishing my laboratory and continues to be an essential resource for our research,” Daniel Hallinan, an associate professor in chemical and biomedical engineering, said. “Some of our most exciting experiments would not have been possible without their assistance. The staff are an immense asset to the college regarding student learning and research progress.”
“They go far beyond a typical machine shop by providing extensive support during the design stage of developing custom devices and parts,” Hallinan said. “They have built numerous, high-quality parts essential to my group’s research, including heating plates, sample holders and cutting-edge instrument accessories.”
Rajan Kumar, a professor of mechanical engineering and director of FCAAP, said, “The FCAAP/AME Machine Shop is a critical part of our research efforts in the polysonic wind tunnel. We have projects requiring custom design and precision that couldn’t be done without their support. We are fortunate to have this resource at the college. The machinists, in particular, Jeremy, have a magical touch to turn a piece of metal into a wind tunnel model of a next-generation flight vehicle.”
Kumar continued, “I often tell our project sponsors that our machine shop is second to none, and the precision of our test articles is always the best in the industry.”
The Machine Shop has two locations on campus. They are in Building A at the FAMU-FSU College of Engineering and the Florida Center for Advanced Aero-Propulsion in the Aero-Propulsion, Mechatronics, and Energy (AME) Building. Their services are free for students, faculty and staff.
RELATED ARTICLES
Engineering professor collaborates with researchers on artificial muscles
Aspiring Engineers Bring Robotic Competition to FAMU-FSU Engineering