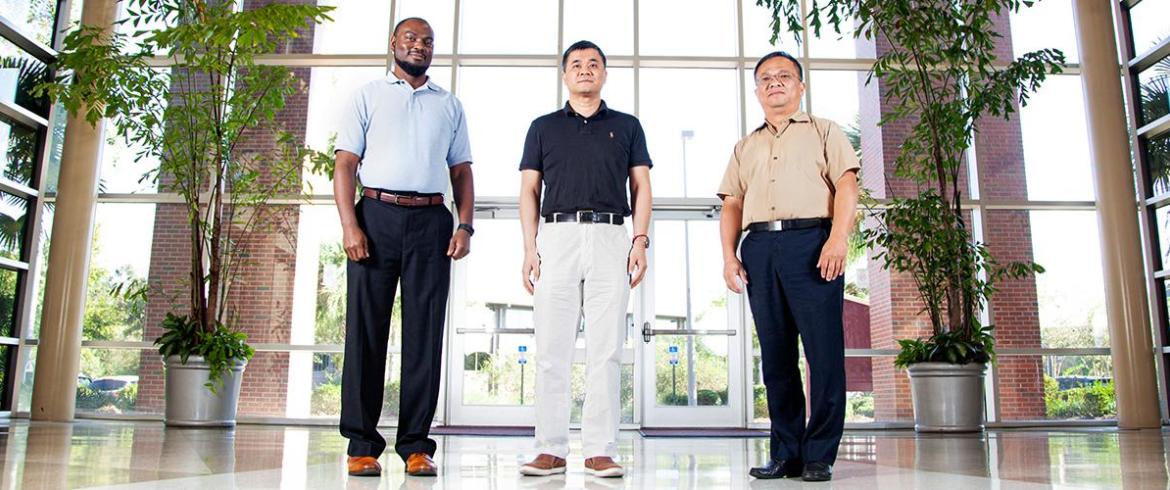
Professors Tarik Dickens, Chad Zeng and Richard Liang
From nanoparticles all the way to outer space, engineering faculty are developing the materials and manufacturing of the future
The High Performance Materials Institute (HPMI) is a “village” that utilizes the talents of its multidisciplinary researchers to create and refine cutting-edge materials to revolutionize science and commerce. It’s also the main research center for the FAMUFSU College of Engineering’s Department of Industrial and Manufacturing Engineering (IME).
Not just one of the foremost resources for the development of novel materials, HPMI also seeks to create and refine manufacturing techniques in order to produce them in a way that is cost-effective as well as reproducible in real-world situations.
As part of a Tier 1 research university, the FAMU-FSU Engineering faculty and scientists affiliated with HPMI work on a wide range of individual projects and have attracted millions in grant money as well as state-of-the-art lab equipment. But its leadership also prides itself on the interdisciplinary collaboration, industry involvement and student participation engendered within HPMI.
“The HPMI is known for our collaborative environment,” said Zhiyong (Richard) Liang, Ph.D., director of HPMI and a FAMUFSU Engineering faculty member. “Each lead researcher has their independent area but there is a lot of interaction to try to collaborate in new ways. Also, we share all the equipment here, which makes for very effective research. And it’s good for students’ education. They can access all the equipment we have.”
The main research laboratory for several high-profile scientists, the HPMI is located in the Materials Research Building, a short walk from the college.
Liang’s research experience and expertise are in the areas of advanced composites, multifunctional nanomaterials and carbon nanotube materials. The importance and uniqueness of his research has attracted significant research funding from government agencies and corporations and, as principal investigator or co-principal investigator, Liang has worked on more than 60 research grants and holds about 25 U.S. patents and pending applications.
HPMI’s leadership also prides itself on the interdisciplinary collaboration, industry involvement and student participation engendered within the research center.
Since size and shape of nanoparticles often determine their functionality in applications, an urgent need exists to design a “well controlled” nanoparticle production protocol that produces large quantities of nanoparticles of uniform sizes and shapes or at least a narrow distribution in both.
Chiwoo Park, associate professor of industrial and manufacturing engineering at the HPMI, is funded by the Air Force Office of Scientific Research to investigate a better way to make consistent carbon nanotubes on a large scale. This research involves developing a dynamic, data-driven control method for controlling the size, shape and composition of a nanoparticle population during production. This research could save time and money in processing nanoparticles.
Liang currently directs the FSU component of a NASA STRI research project (see opposite page) to develop carbon nanotube-based structural materials to create next-generation space vehicles and potentially even space habitats.
Space might be the place for products and processes created via the research of Tarik Dickens, Ph.D., whose area of expertise is additive manufacturing— commonly known as 3-D printing. His dexterous robotic printing agents provide an avenue for intelligent processing—and building—of new components.
“I’m also part of the NASA project,” Dickens said. “We’re trying to design next-generation materials that will take us to Mars. When we get to Mars—or even before we get there—we need to have habitats and working equipment. 3D printing will likely be part of that.”
Having a 3D printer available on the Red Planet would also be useful, he said, to create needed tools or materials, “since a run to Home Depot for a missing wrench or part wouldn’t be in the cards.”
But the additive manufacturing technology has more down-to-earth commercial applications—custom made footwear, for example.
Dickens also leads students in the interdisciplinary National Science Foundation Center of Research Excellence in Science and Technology (CREST) and the HBCU Research Infrastructure for Science and Engineering (RISE) program, developed to encourage minority and female undergraduate and graduate students to consider careers and advanced schooling in the STEM fields.
CREST-RISE supports the education of graduate students and sponsors a well-attended summer Research Experiences for Undergraduates program leveraging the resources of the HPMI.
Important, said Liang, because most students don’t know much about materials and manufacturing before they arrive.
“We try to provide many opportunities to the undergraduate students and let them get into the lab, hang out with professors and grad students and see different projects,” he said. “We give them time to figure out what materials research is and to learn about manufacturing research … This can attract them to engineering research as a career.”
One of the greatest success stories is told by Changchun (Chad) Zeng, Ph.D., an associate professor and director of graduate studies for the IME department. When he came to the college in 2007, he was intrigued by a new type of foam first described by a physics professor in the 1980s.
But it would take until 2011 before Zeng got the grant funding from the Department of Veterans Affairs to research “auxetic” foam. The agency was searching for ways to provide better health care for veterans, especially those with prosthetic limbs. He proposed to create auxetic foam, which does not thin out when it is stretched but instead expands, enabling it to provide better protection and stabilization. The material could be used to make prosthetics conform better to an individual’s anatomy, which would in turn relieve pressure points and make them more comfortable.
Zeng and his team were able to create and patent the unique material and develop a process that would allow it to be produced commercially.
“Often, when knowledge comes out of the university, it’s usually more like a concept,” Zeng said. “It’s a product that works, but it doesn’t work every time. It may not be the most economically efficient way to make it. But this one, it works. It works every time. And the process is very, very efficient.”
The auxetic foam was licensed to Auxadine, a Florida-based startup company, which manufactures the foam for commercial use and now sells a line of medical products including seat cushions, orthotic shoe insoles, wheelchair pads and other therapeutic products.
Other manufacturers are using the foam to create protective products for athletes. In fact, auxetic foam has come full circle back to its birthplace. Players for the Florida State University football team are wearing supportive braces made with the foam and Zeng was surprised to discover Jessie Warren, who led the Seminoles softball team to a national championship win in 2018, was wearing an ankle brace lined with auxetic foam.
Zeng’s work with auxetic foam is far from over. The foam is also being tested for use as the protective liner in football helmets to improve player safety, thanks to a grant received by the licensee Auxadyne from the National Football League. He also envisions helmets having foam coated with sensing nanomaterials such as carbon nanotubes which could immediately measure the force of an impact and where it occurs.
Zeng’s team is also working on different types of auxetic foam, either harder or softer. Sturdier auxetic foam could be used for body armor. But what Zeng is excited about is the creation of a softer version that can be used as a “scaffold” to help turn stem cells into, for example, neuron cells, heart cells or brain cells.
This summer, Zeng was a collaborator with FAMU-FSU Engineering colleague Yan Li, Ph.D., a stem cell researcher, on a proposal that received a three-year, $400,000 NSF grant to develop an auxetic foam that could be used in such tissue engineering.
“If it works as we think it will, it’s going to open a floodgate,” he predicted. “Basically, it gives you a completely new way of manipulating cells to become certain type of tissue.”
The tissue created using stem cells and the foam scaffold could be used in medical research to treat cardiovascular conditions or Alzheimer’s disease.
“It has potential,” Zeng said. “We are the only one that can generate this type of scaffold that will provide the ‘living environment’ and mechanical stimulus for these cells to grow.”
HPMI director Liang also emphasizes the value of the institute’s relationships with many governmental agencies and Fortune 500 companies such as NASA, Lockheed Martin, Intel, Boeing, Dow Chemical and Northrop Grumman.
“Because we work side-by-side with industry and government research teams, we see the real-world problems,” he said. “We strive to improve their products, particularly for some critical materials they need. We support them with our analytical capability and expertise and, in turn, try to understand their manufacturing process.”
Liang points out another benefit of these relationships: “We also expose our students to industry collaboration. Students can talk with these industry people. It prepares them to go into the real world.”