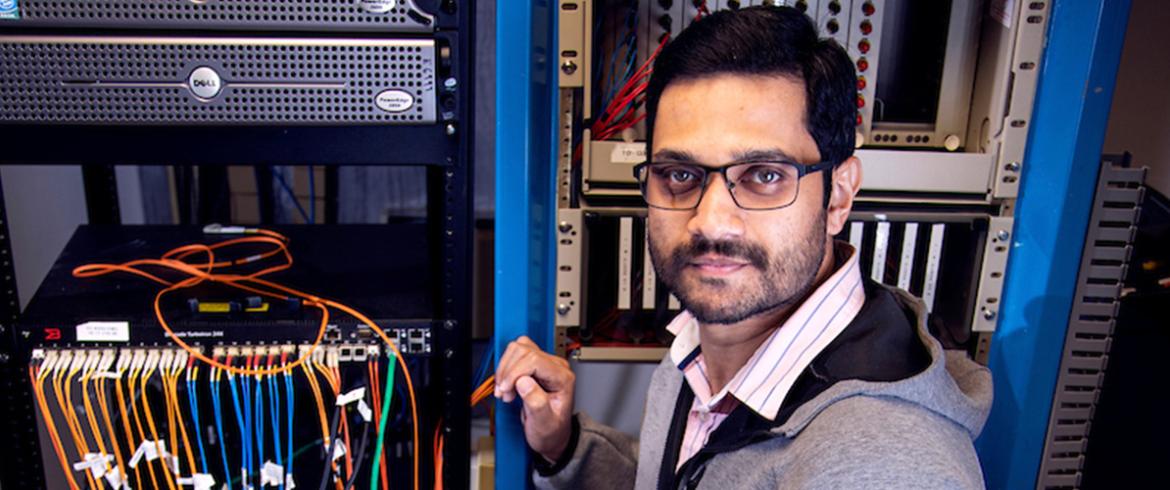
Assistant Professor of Mechanical Engineering Unnikrishnan Sasidharan Nair.
In a region of the United States that is home to 20 major military installations and a defense business presence worth $95 billion annually, the FAMU-FSU College of Engineering is uniquely situated for high-impact aerospace research and testing.
Florida hosts two (of only four) deep-water naval ports with adjacent airfields, the Joint Gulf Range Complex in the Gulf of Mexico, the military’s only east coast space launch facility and several critical Department of Defense (DoD) research, development, training and evaluation (RDT&E) centers. Of those, the majority are located in the northwest region of the state, within a short distance of the college.
This backdrop provides a rich atmosphere for commercial aerospace and defense-related engineering research to thrive. In addition to close contacts with key defense stakeholders in the research frame, the college also enjoys collaborative research efforts with defense-industry public and private businesses including Boeing, Lockheed Martin, BAE Systems and Raytheon.
For a college and mechanical engineering department with its sights set on becoming a nationally-recognized hub for aerospace research, there is likely no better place than Tallahassee and Leon County’s Innovation Park, adjacent to the campus.
FAMU-FSU Engineering is already surging ahead in the field, with the Florida Center for Advanced Aero-Propulsion (FCAAP), a state-recognized and supported Center of Excellence whose research has had a major impact on the space and aerospace industry in Florida and beyond. With its trio of high-tech (and high-speed) wind tunnels, high-temperature jet and short take-off/vertical landing aircraft (STOVAL) facilities, FCAAP is the site for mission-critical engineering test model research by mechanical engineering faculty such as Louis Cattafesta, Rajan Kumar and others.
A relatively new area for the college is computational fluid dynamics (CFD), brought to the department by junior faculty members emerging in their field as highly creative and prolific researchers. Assistant Professor of Mechanical Engineering Unnikrishnan Sasidharan Nair joined the faculty alongside his colleagues Neda Yaghoobian and Kourosh Shoele, both also assistant professors in mechanical engineering focused on advanced, multi-physics CFD.
From Algorithm to the Field
Historically, the faculty at FCAAP and other college-associated centers have focused on materials science and experimental aerodynamics, leveraging our advanced wind tunnels and other test facilities.
These recently-hired mechanical engineering researchers are interested in advanced computational fluid sciences, which is an area that includes simulations, mathematical models and other research methods fine-tuned to the study of fluid-thermal systems, including aerodynamics.
Using algorithms and computer models to solve equations that predict fluid flow, for example, researchers develop simulations which offer low-cost pre-test environments for defense-related concepts. Once a design is established, computational research can develop algorithms and apply advanced mathematics to evaluate critical performance parameters before a model is built out and ready for the wind tunnel.
“In one study, we are simulating air flow in the context of high-speed aircraft,” Sasidharan Nair explains. “This can help define the size of the wings and other parts of an aircraft (before they enter the costly design and test phase).”
In a series of recent grants totaling $1.4 million, Sasidharan Nair is pushing forward on computational aero-sciences as a new research thrust at the college, complementing his colleagues’ work in similar engineering areas.
As a mechanical and aerospace engineer in the aerodynamics field, Sasidharan Nair is specifically interested in the design of aircraft components that move through the air at very high speeds. How does air behave as a compressible-fluid as it flows over the aircraft? What principles of fluid dynamics apply and how can they be harnessed to mitigate environmental, health and physical impacts of these machines on crews and communities?
Mitigating the Boom
Aero-acoustics refers to the study of sound and associated fluid dynamics, and is a key discipline utilized to evaluate the noise emitted by military aircraft as they soar through the air. In one study for the U.S. Navy, Sasidharan Nair and his team are determining how the acoustical properties of those aircraft behave differently at supersonic speeds and in different atmospheric conditions likely encountered at high altitudes.
While common to communities in Northwest Florida, the traditional “sonic boom” emitted from military jets as they break the sound barrier at supersonic speeds can negatively affect humans and wildlife.
According to JSTOR Daily, sonic booms aren’t just loud; they can also cause physical damage, breaking glass, cracking plaster and shaking objects off shelves. A boom from a single fighter aircraft in 1966 dislodged tons of rock, crushing archaeological sites in the famous Canyon de Chelly National Monument. In addition, the U.S. military acknowledges that the shock waves cause ear and hollow cavity damage to human bodies.
Right: Simulation of the turbulent plum ejected by a supersonic jet. Left: A zoomed-out image of the jet highlighting its acoustic emissions. (Courtesy Sasidharan Nair)
Because of its deleterious effects, the U.S. military is interested in ways to mitigate the boom itself—perhaps by designing aircraft that create smaller “booms” during supersonic travel. A key milestone in advancing civil aviation in the near future will be the reintroduction of supersonic flight—similar to the Concorde, but in a more environment-friendly and sustainable manner. For supersonic commercial aircraft to be practical they must be able to fly at supersonic speeds overland, something the Concorde could not due to its very loud sonic boom. Hence the challenge is in how to design efficient commercial supersonic aircraft where the aerodynamic and propulsive design is boom-constrained.
To better control the sound emissions from aircraft, Sasidharan Nair is looking at the noise-sources involved in the traditional sonic boom, as well as the “shock-dominated jets” that often accompany them as the high-temperature, high-velocity exhaust from jet engines create differences in pressure that are mismatched with the surrounding atmosphere. These characteristic “shock cells” in these jets create sound signatures in addition to the sonic boom. Their extremely high temperatures and pressures make it very difficult to predict their behavior and their acoustic impact on ground crew. For U.S. Navy aircraft carriers where humans and jet engines are always in close proximity, understanding and mitigating these impacts is a priority.
To attack this problem, Sasidharan Nair has developed algorithmic tools to exactly predict how much sound is generated from this complex flow system of military plane exhaust. His model includes some of the most advanced algorithms available and is part of the reason he was chosen for the study.
Sasidharan Nair’s work on simulating the complex dynamics of shock cells and characterizing the acoustics of military tactical aircraft, particularly Naval aircrafts, dovetails nicely with the state-of-the-art experimental high-speed jet aero-acoustics research performed steps away at FCAAP.
“We have to validate our algorithms and calculations against wind tunnel and jet-rig test data,” he says. By creating and testing a model component in the Mach-5 polysonic wind tunnel, the team is able to validate or fine-tune their algorithms for the military.
Creating techniques to control sound emissions is ripe with possibilities, including using actuators in the system. Active control, as it’s known, excites the engine exhaust to achieve a lower acoustic impact and better match the atmospheric conditions. There are multiple possibilities for the future of acoustic mitigation, and these studies are an important step in that direction.
To Sasidharan Nair’s mind, having FCAAP and highly and uniquely capable facilities he needs so close is where the real nexus is found.
“While computational aerodynamics and acoustics provides the depth of study, the jet noise anechoic chamber provides actual data with more generalizable details,” he says.
The Blurry Line of Hypersonics
While the term “hypersonic” is a bit hard to define—there’s no sharp boundary between super- and hypersonic regimes—for aerospace research it’s generally accepted as any craft traveling 5 times the speed of sound (Mach 5) or faster. Currently, the realm of unmanned concept vehicles including rockets and missiles, sustained hypersonic flight has great potential and many challenges. At speeds this fast, materials burn up and the air begins to act more like a reacting plasma than an unreactive gas. Despite challenges, the U.S. military and commercial aviation industries have their sights set on even faster speeds—above Mach 6.
In a 4-year collaboration with The Ohio State University, Sasidharan Nair and his team are working to computationally mitigate the distortion of boundary layer profiles (of velocity), a major challenge in designing hypersonic aircraft. This boundary layer is the region on an aircraft wing where air “sticks” as it flows over the surface, causing internal friction in the air to heat the surface. Much like the turbulent flow of water from a faucet that causes it to spray out from its downward stream, irregularities in the surface of aircraft systems can affect the boundary layer, causing it to transition from a laminar to a turbulent state. For example, when the faucet water is a smooth column flowing outward, it is considered laminar. However, once the water “catches” on a scratch inside the faucet fixture, it results in a turbulent zone that produces a scattered “spray” at the end of the flow.
Simulation of the air flow inside an inlet of a supersonic aircraft. (Courtesy Sasidharan Nair)
In aircraft systems, the heat and drag loads are manageable and limited when the flow is laminar. However, these exceed safe thresholds when the flow transitions and becomes turbulent, resulting in surface damage. To realize safe, manned, hypersonic aircraft, this laminar to turbulent transition must be managed. With his collaborators, Sasidharan Nair aims to help identify materials or mechanisms to mitigate surface damage due to transition at hypersonic speeds.
Sasidharan Nair’s computational models seek to help understand — and describe — the mechanics of the transition. Then, they can better describe the optimal shape, design and materials for aircraft components where these flows are encountered.
“We want to avoid the dangerous transition to turbulence or at least move it further down the vehicle,” he explains.
Tweaking Geometry for Better Design
In another computational-to-test collaboration, Sasidharan Nair and Rajan Kumar, associate professor in mechanical engineering and FCAAP director, are studying the optimal design for a supersonic jet engine inlet. The co-PIs believe the research could help end disastrous engine failure events.
In traditional subsonic aircraft, turbines compress the air prior to combustion inside the engine. In supersonic aircraft, however, the inside surface of the air intake conduit “bends” the high-speed air to create shocks that compress the air flow in a highly efficient process that super-concentrates air-density to a level required by the engine. While this is one of the innovations of jet design, the sometimes-violent breakdown of this compressed air stream into the engine results in a deadly “unstart,” or engine failure event.
“If we can tweak the geometry of the inlet’s internal design,” Sasidharan Nair says, “we can produce a more robust inlet shock train that will mitigate these back-pressure variations, making them less sensitive to disturbances.”
Back to Basics
In addition to these military applications, Sasidharan Nair’s computational approaches and FCAAP’s aerodynamics research facilities are being used for work on fundamental fluid dynamics. In a research and development project, Sasidharan Nair is looking at fundamental questions involving hydrodynamic stability and the aerothermal chemistry of fluid dynamics. He’s asking what causes instability in fluid flows, as well as what makes fluid systems challenging to predict; and what are the aerodynamic, chemical and thermodynamic properties of high-speed flows?
“I had the opportunity to leverage my startup funds when I joined the college in 2019,” Sasidharan Nair says. “Now we are working on grants that will affect and inform various parts of aircraft design for the future, like inlets, exhausts and wings.”
With the funds, he created the algorithmic prototype tools that were the basis for these military and R&D grants. It was, he believes, his contribution to the burgeoning computational aerodynamics and aerospace research center that will soon be a reality.
Farrukh Alvi, senior associate dean for research and graduate studies and mechanical engineering professor, agrees.
“Unni’s work complements and leverages our current work in high-speed aerodynamics and jet aero-acoustics, and our strong computational skills in the field,” he says. The computational and experimental team in mechanical engineering now routinely tackles multi-scale, multi-physics projects.
The dream is still to become a computational center of excellence, but that’s for others to bestow. FAMU-FSU Engineering is already in the top 10 nationally for high-speed experiential aerospace research with its FCAAP facilities, and Sasidharan Nair’s work is a great complement and extension to that.
“We are not as big as some others but we are very efficient for our size,” Alvi contends. “This work is a big step toward our goal to become the leading center that addresses high-speed aerodynamics for commercial and defense applications.”
With the rich groundwork laid by Kumar, Cattafesta, Shoele, Yaghoobian and a host of others in the mechanical engineering department, the opportunities seem endless for collaboration and innovation in the aerospace sector.
“Our work college-wide in these areas, combined with our advanced materials capability, make us holistically suited for more and more of this work going forward,” Alvi says.