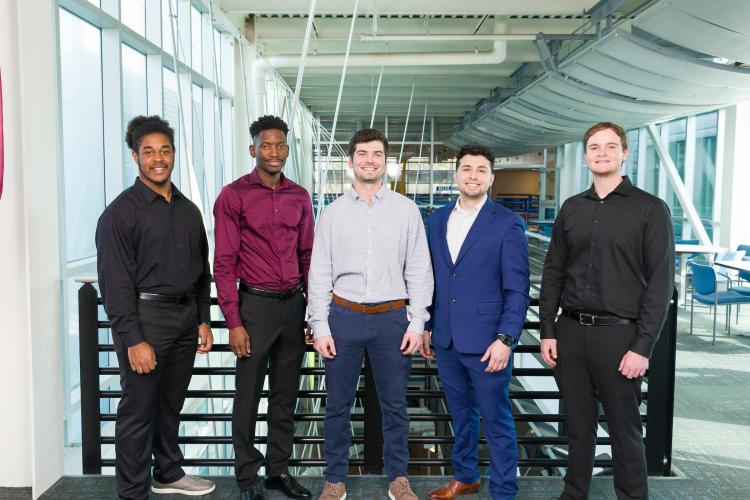
Corning aims to improve its diesel exhaust filter production line by creating an automated pallet topper machine that can stack filters without human help. Currently, employees place and remove the final pallet on a stack of filters. By adding an automated pallet topper, workers can focus on other parts of the production line, making the workflow more efficient. Corning seeks a project that can complete the placement of the final pallet topper in a suitable amount of time.
After examining Corning’s production line, we designed a scaled pallet gripper that can move horizontally and vertically to place pallets on a flat surface. The scaled pallet topper uses a frame with rails, bearing blocks and air pistons to create motion. The horizontal motion moves the pallet to a new location, while vertical motion moves it up and down. An air gripper attached to the vertical rail picks up and releases the pallet.
We created a full-size computer model to demonstrate the automated pallet topper in Corning’s production line, helping estimate performance speed. The scaled version shows how the full-sized model could move.
Corning values this project since it will increase production performance. The automated topper will remove employee engagement, reduce physical strain and speed up manufacturing. It will lower production costs by reducing labor expenses, allowing employee reassignment elsewhere. This automation will enable Corning to keep up with demand, improve quality and maintain a competitive edge.
Ahmari Avin, Brightson Bazile, Daniel Mack, Michael Rodriguez Capera, Craig Yox
Christian Hubicki, Ph.D.
Corning
Spring