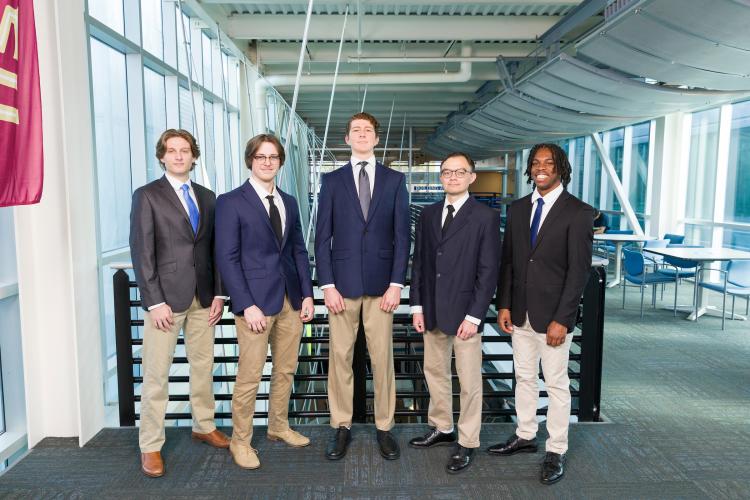
We aimed to create a vehicle capable of gliding underwater and collecting data. Inspired by other underwater vehicles, we wanted to simulate an underwater glider. We built a physical model to check the accuracy of the simulations. The glider collects data similar to those collected by gliders in other industries, such as water pressure and temperature. The defense industry makes use of underwater gliders for intelligence collection. They often use long-endurance vehicles to collect vital information to aid national defense. Another field that has used the technology is oceanography, where gliders have tracked weather patterns that would otherwise be difficult for a human to capture.
We used various computer simulations to evaluate the final design. We ran simulations via MATLAB to calculate the best path for glider motion. To control the glider’s movement, motors control both dive planes influenced by sensor data. We simulated dive planes using SOLIDWORKS Flow Simulation toolbox and Autodesk Fusion to evaluate water flow. The glider has a unique double-cylinder setup that helps prevent instability experienced underwater. We built the glider through 3D printing and coated the surface with epoxy. This seal stops leaks and makes the glider smooth.
Following an up-and-down pattern, the glider moves in swimming pools and freshwater environments. It goes down to a depth of ten feet and performs assigned tasks. The glider collects data during its dive. The glider’s movement comes from propellers that act in place of buoyancy engines. We uploaded the data to a computer and compared it to simulations.
Jake Burns, Tristan Hardy, Nicolas Lorin, Justin Sepulveda, Martin White
Kourosh Shoele, Ph.D.
Boeing
Spring