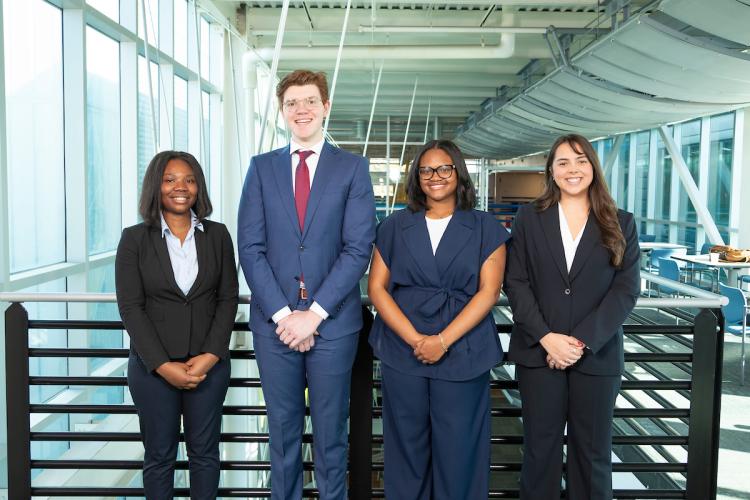
With plans underway for establishing a crewed outpost on the Moon, the need for innovative construction methods is paramount, especially given the astronomical costs associated with transporting materials from Earth. The cost of launching payloads to the Moon using the Space Launch System (SLS), estimated at over $75,000 per kilogram, underscores the urgency for alternative, cost-effective solutions.
In-situ resource utilization (ISRU) and additive manufacturing (AM) using lunar regolith have emerged as promising avenues for sustainable lunar architecture and equipment production. ISRU presents a viable approach to leveraging local resources, in this case, lunar soil and biologically available binders, urea, sodium alginate, and methylcellulose, as a potential reduction of the reliance on Earth-sourced materials. Among the potential applications, lunar regolith-based AM technology offers a promising avenue for constructing habitation and equipment on the lunar surface since it is seen as a replacement for Ordinary Portland Cement.
This study examined the feasibility of laser-based additive manufacturing for lunar applications, focusing on the utilization of lunar regolith as a primary material. Chemical and geological characteristics of lunar regolith, coupled with operational considerations for AM technology in lunar environments, are thoroughly explored. By assessing the viability of AM with lunar regolith, this study contributed to the development of cost-effective and sustainable construction practices for future lunar missions.
Elizabeth Owojuyigbe, Anthony Psulkowski, Zaire Shaw, Isabella Sheffler
Tarik Dickens, Ph.D. and Ernesto Garcia, Ph.D.
NASA Marshall Space Flight Center
Spring